Real-time location systems (RTLS) for manufacturing efficiency
Boost manufacturing efficiency with RTLS technology. By implementing RTLS solutions for manufacturing and logistics, you can optimise workflows, increase production visibility, and reduce accidents between machines and workers. Real-time tracking of assets, equipment, and personnel allows for accurate positioning and timely decision-making. Streamline operations, improve safety measures, and enhance overall performance by integrating RTLS systems.
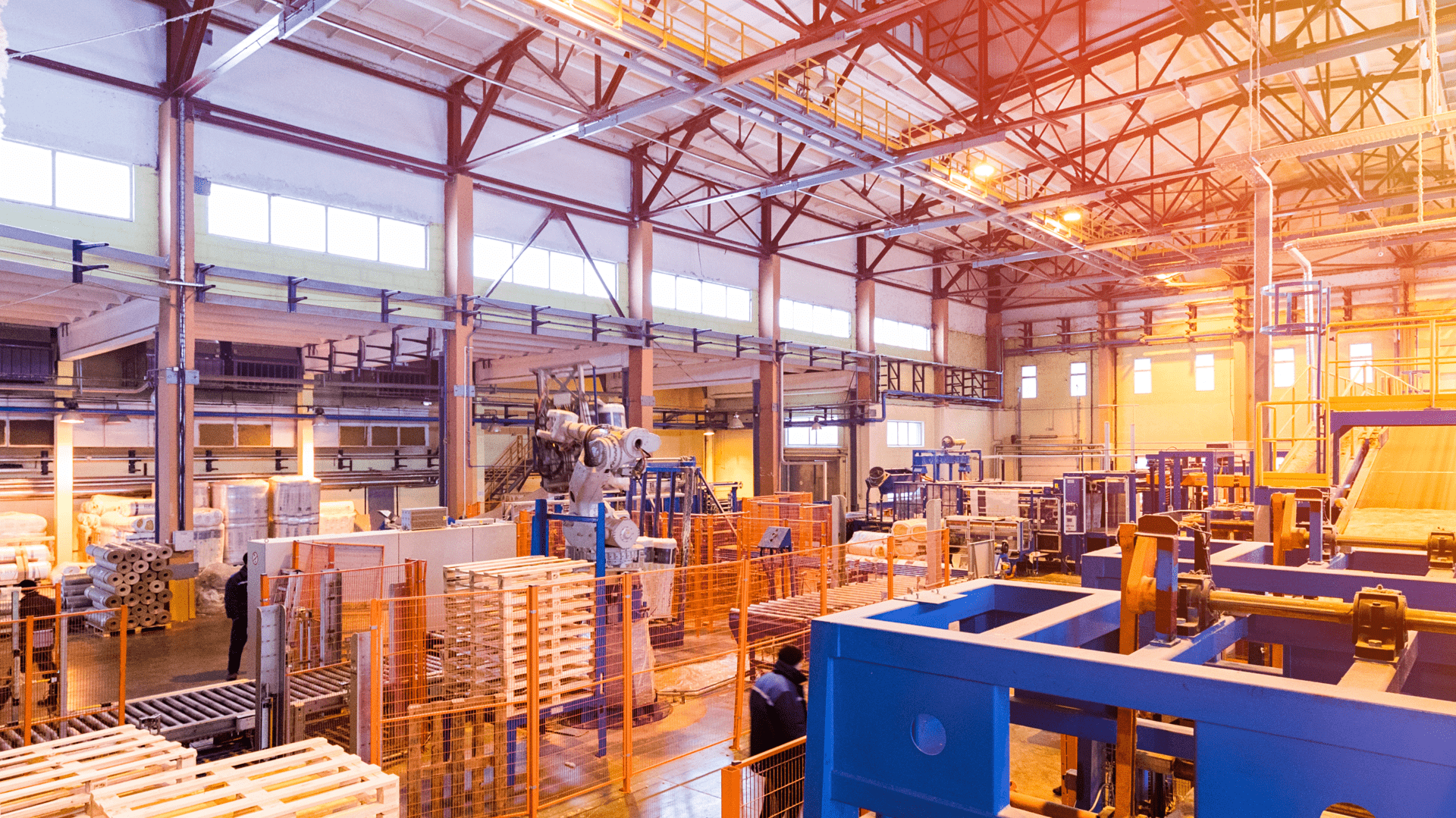
Key benefits of Ubudu hybrid RTLS for manufacturing & logistics
Harness the power of Industry 4.0 to enhance operational performance in manufacturing and logistics. The digital transformation of these industries brings significant benefits. Introducing Ubudu Hybrid RTLS manufacturing empowers you to efficiently address a wide range of Track & Trace use cases while minimising deployment and maintenance costs.
Return-on-Investment (ROI) observed by our customers
Time saved in searching for assets in the factory or warehouse
Takt time reduction through better production visibility
Decrease in equipment spendings thanks to better utilisation rate
Optimise manufacturing operations with RTLS technology: Enhancing efficiency and production processes
In manufacturing, Real-Time Location Systems (RTLS) play a crucial role in accurately tracking the real-time location and status of equipment, tools, and personnel. Utilising a combination of wireless communication technologies such as BLE, UWB, LoRa, as well as dedicated hardware and software components like the Location Engine and End-user Application, RTLS technology provides precise and up-to-date information about asset location and status within manufacturing facilities.
Implementing the Ubudu RTLS manufacturing brings numerous benefits, including improved operational efficiency, minimised downtime, and enhanced safety measures. Selecting the most suitable technology depends on the specific requirements and constraints of each use case. Often, a combination of different technologies may be necessary to achieve optimal results. By leveraging the power of RTLS technology, manufacturers can unlock greater efficiency, reduce costs, and ensure a safer working environment.
Track the location of work orders
Achieve real-time and transparent visibility into your production operations by accurately tracking the precise location of work orders. With our advanced tracking system, you can monitor the progress of work orders in real time and receive automatic alerts for any detected delays. This level of visibility allows you to proactively manage your production processes, identify bottlenecks, and take timely corrective actions. Improve operational efficiency and ensure smoother workflows by leveraging our cutting-edge technology for work order tracking.
Reduce time spent by operators searching for work orders to increase productivity
Show the real-time location of all work orders on a map so that operators don't waste time searching for them.
Avoid production interruptions and delays
Receive real-time alerts by email in case a work order has spent too much time in a specific workstation in order to take the necessary action to avoid any delay or interruption.
Optimise production flow by identifying bottlenecks
Analyse how your work orders move between different workstations, how long they stay in each zone and which path they take between zones to continuously improve your workflow and enhance the production process.
Provide real-time visibility on work order status to your account managers
Account managers can filter by client name all the orders in production to quickly check where they are and therefore understand their status to keep their clients informed and anticipate any delay.
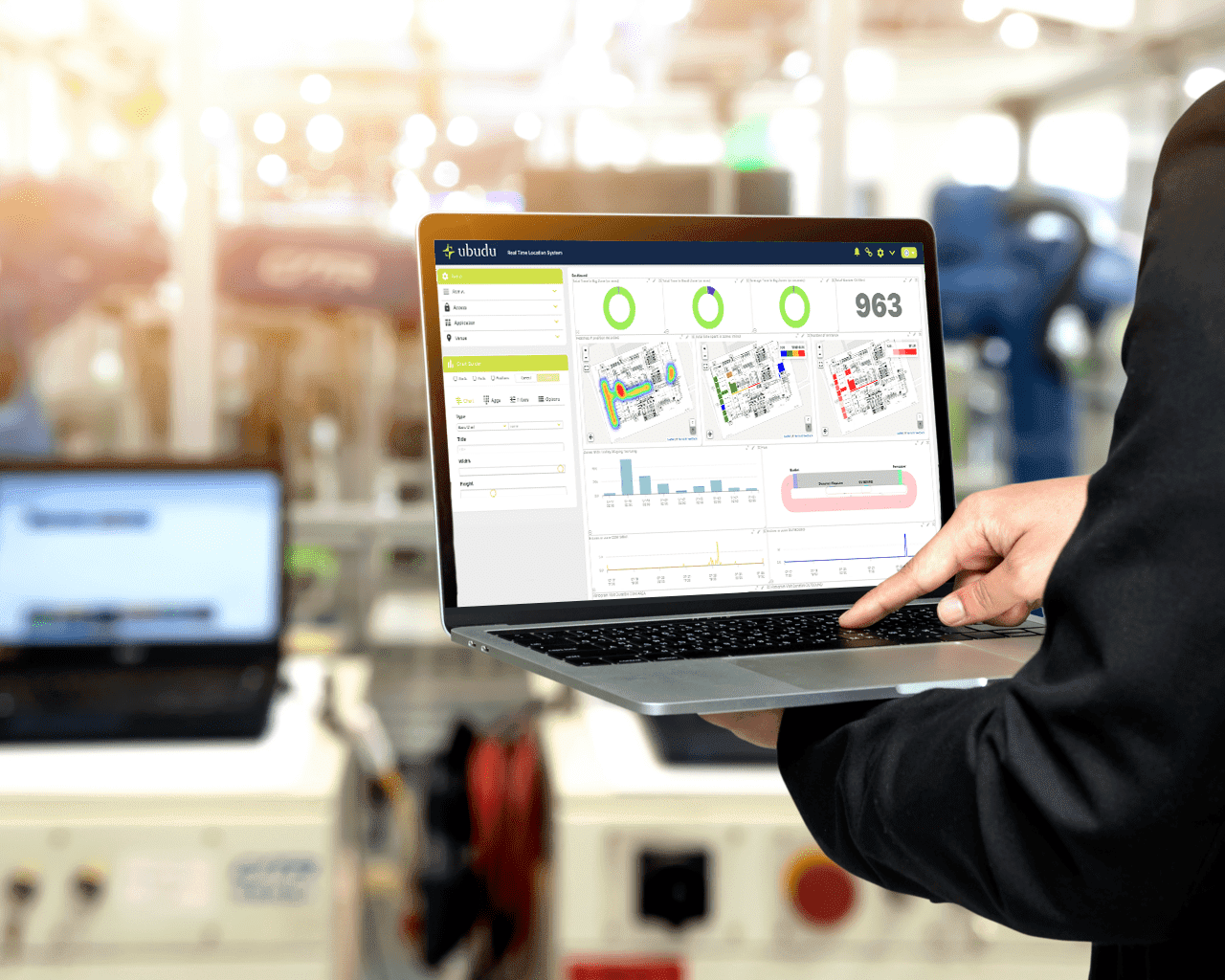
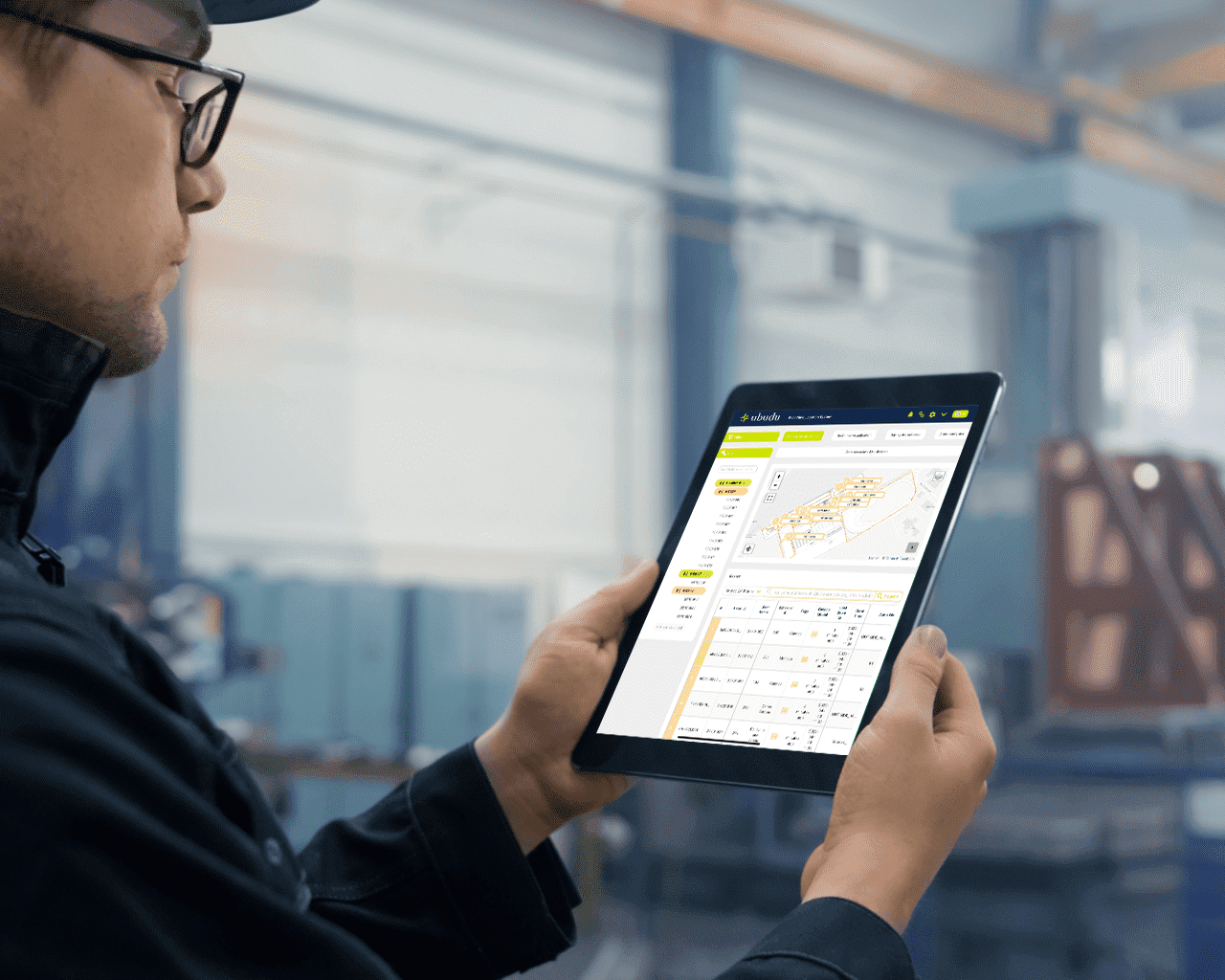
Track the location of tools & equipment
Our RTLS system for manufacturing enables you to monitor the movement data of tools and equipment, allowing you to measure their utilisation rates accurately. With real-time location tracking, you can receive automatic alerts if a tool exits a designated zone or remains idle for an extended period. This proactive approach helps prevent loss, optimise resource allocation, and ensure efficient utilisation of tools and equipment. Enhance operational efficiency and reduce downtime by leveraging our comprehensive tracking solution for tools and equipment.
Reduce time spent by operators searching for tools & equipment to increase productivity
Show the real-time location of all tools & equipment on a map so that operators don't waste time searching for them.
Increase tools & equipment utilisation rate
Analyse the utilisation rates of tools & equipment based on how much time they spend in different zones and how often they move from one zone to another.
Optimise intra-logistics flows
Following a continuous improvement approach, analyse the flows of your Material Handling Equipment (MHE) to optimise their circuits and avoid any material shortage in your workstations.
Enhance worker safety: Real-time alerts and hazard prevention
By leveraging our RTLS solution, workers receive instant alerts about nearby hazards, enabling them to take immediate precautions. In the event of an emergency, our system ensures the safety of all staff by providing real-time notifications and guidance. Prioritise worker well-being, mitigate risks, and maintain a safe working environment by implementing our cutting-edge safety solution.
Avoid accidents between machine and workers
Send a real-time alert to pedestrian workers and machine operators when they get too close to each other to prevent collisions.
Better control access to hazardous areas
Remind workers of the danger in the hazardous area before they enter through a real-time alert.
Locate workers in case of emergency
Ensure all your workers have evacuated the area where an emergency or accident happened to avoid leaving anyone behind.
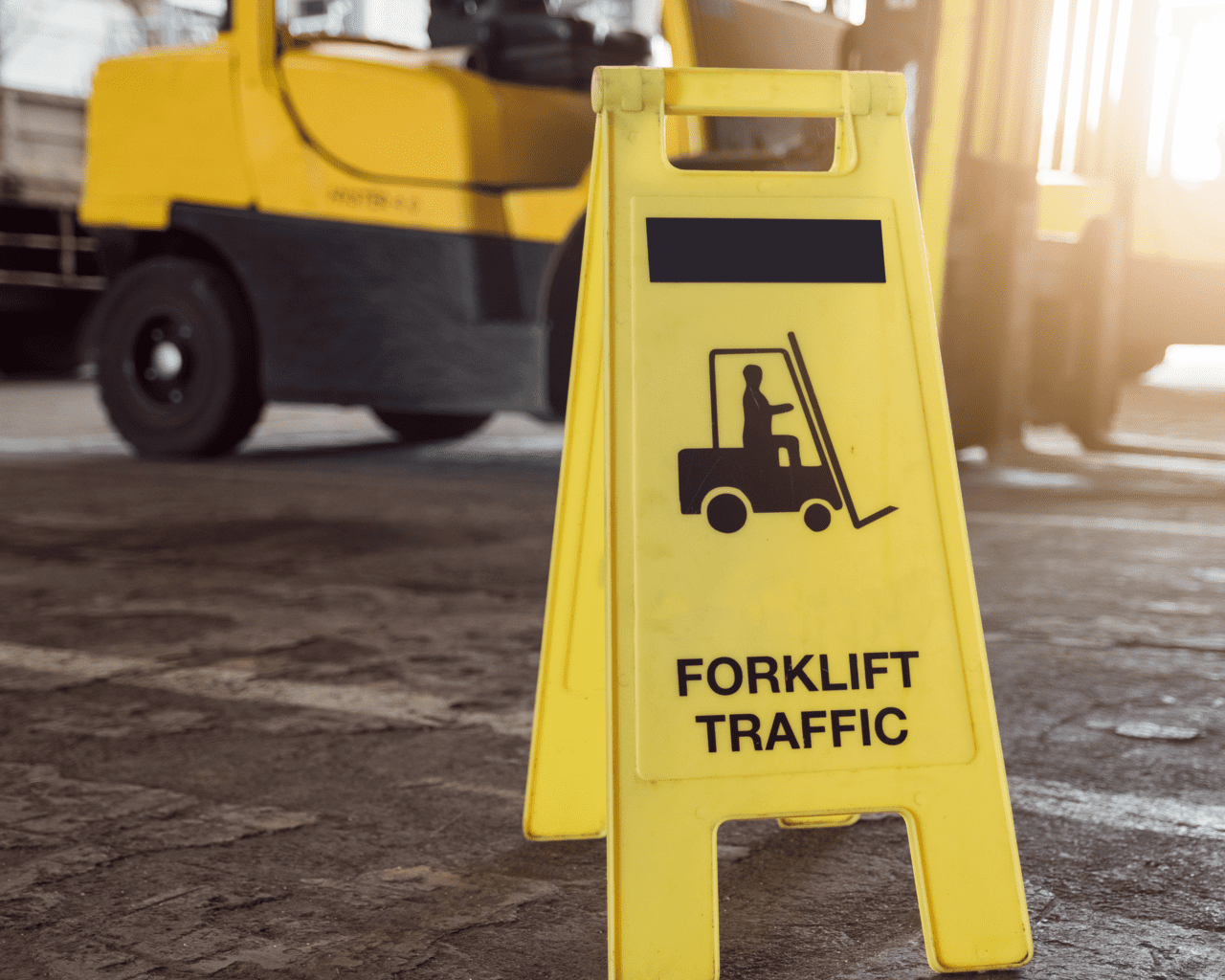
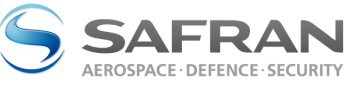
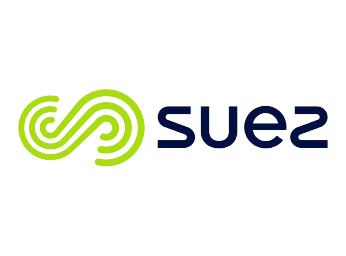
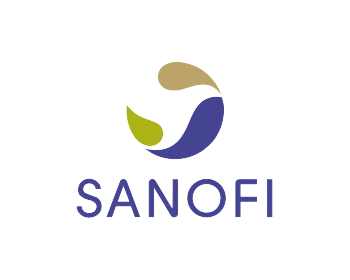
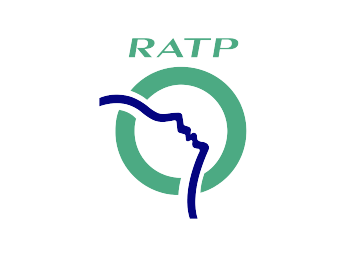
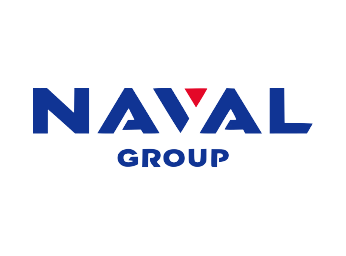
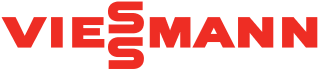
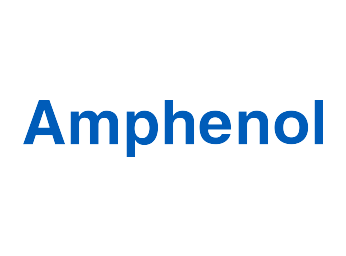

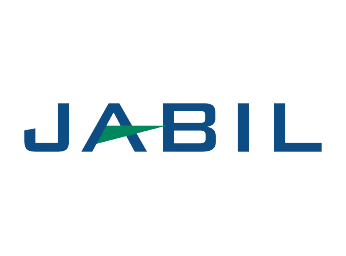
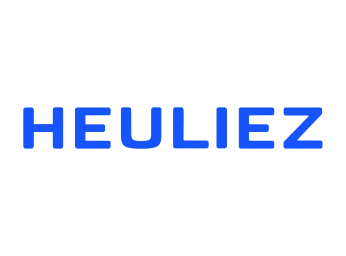
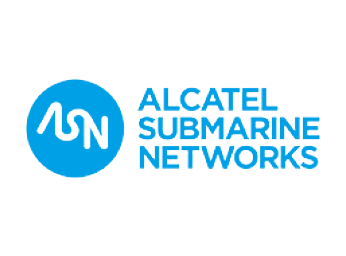
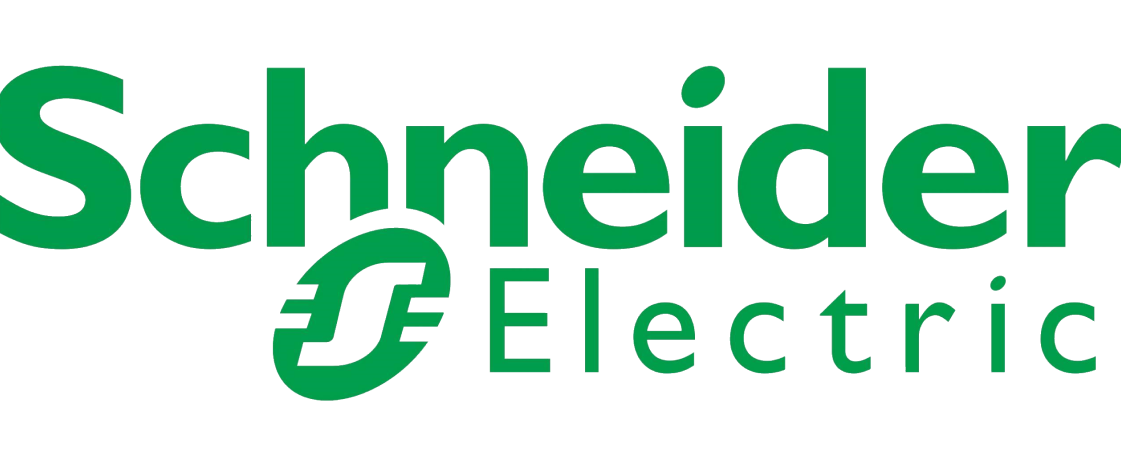
Ubudu RTLS: The Ultimate Tracking Solution for Different Industries
Ubudu solutions are tailored to meet diverse needs across a range of industries. From optimising operations and enhancing visitor experiences to improving asset traceability and worker safety, our versatile solutions provide efficient and effective results.
RTLS for Manufacturing & Logistics
Make your operations more efficient by optimising operational flows and increasing visibility on production.
RTLS for Quick Service Restaurant
Avoid time wasted by waiters searching for customers at their table and make your customer experience more seamless.
RTLS for
Healthcare
Make it easy for your staff to find equipment they need, reduce yearly expenditure on new equipment and improve patient satisfaction.
RTLS for Construction
Optimise the usage of expensive machinery on-site and reduce the risk of accidents caused by collisions or hazardous zones.
Made in-house and designed in Europe, get to know our products.
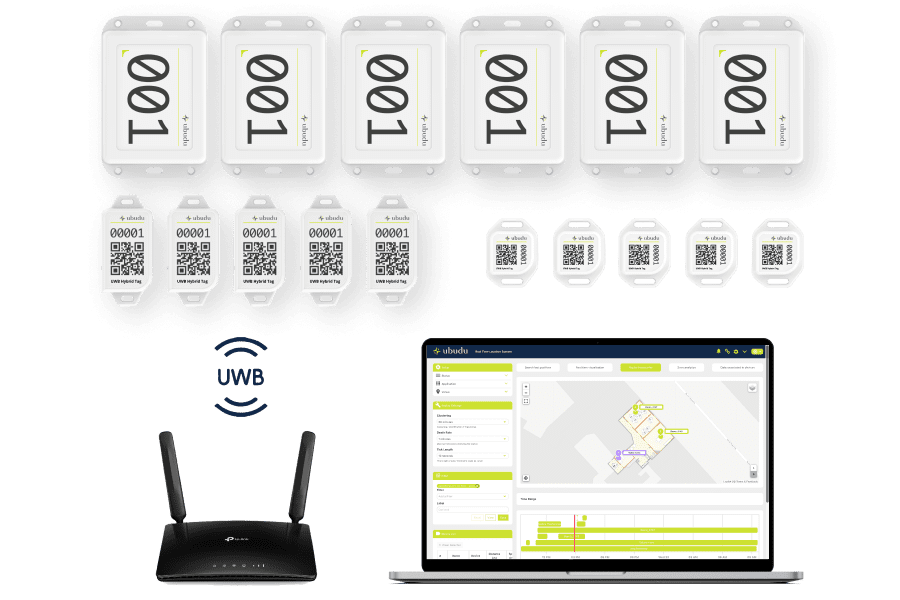
Plug-and-play Starter Kits including Ubudu hardware, software, tools and documentation in order to let you test and show demos of Ubudu RTLS in no time.
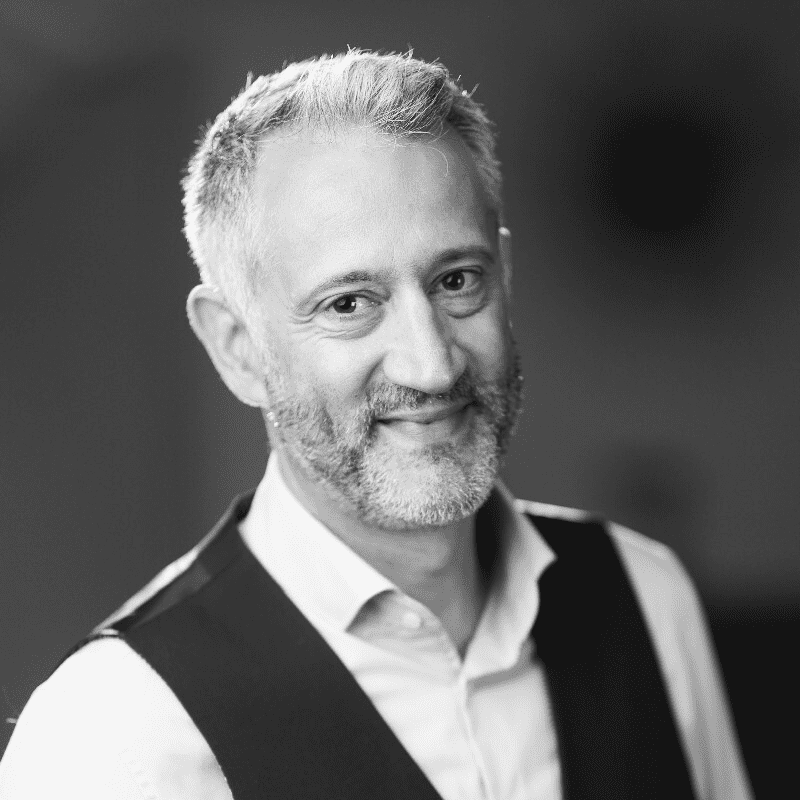
Ubudu's RTLS solution provides beneficial functionality through a combination of technologies and a platform that simplifies data analysis. Thank you to the technical and sales teams for their responsiveness and efficiency.
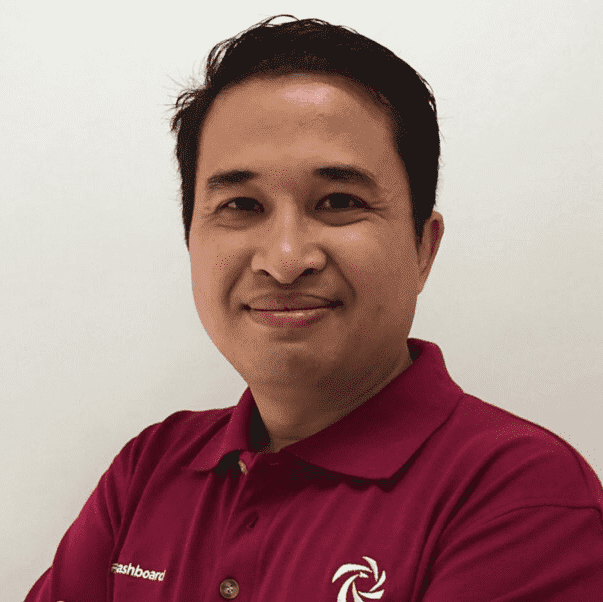
We are proud to be working hand in hand with renowned tech company Ubudu in bringing SDA+ and RTLS into the SM4RT TRACE suite of solutions. Thanks to Ubudu’s expertise and experience with the technology itself, we are able to make Malaysian offices, factories and warehouses safer and more efficient.
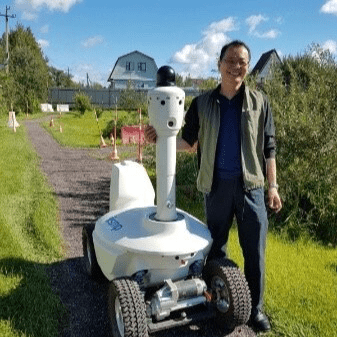
Ubudu hybrid RTLS platform provides us the necessary flexibility to go-to-market and address different customers’ needs with competitive offerings. With its out-of-the-box applications and tools, the solution is easy to deploy and customer onboarding is smooth.
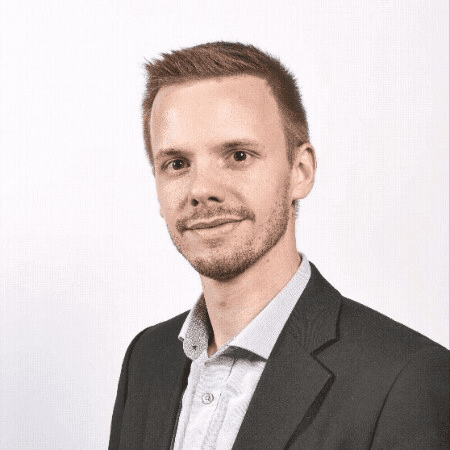
Ubudu has enabled us to secure pedestrian movements in our sorting centres in a simple, quick and large-scale way. This solution is more easily adopted by our employees, unlike the more expensive and limited solutions we had previously deployed.
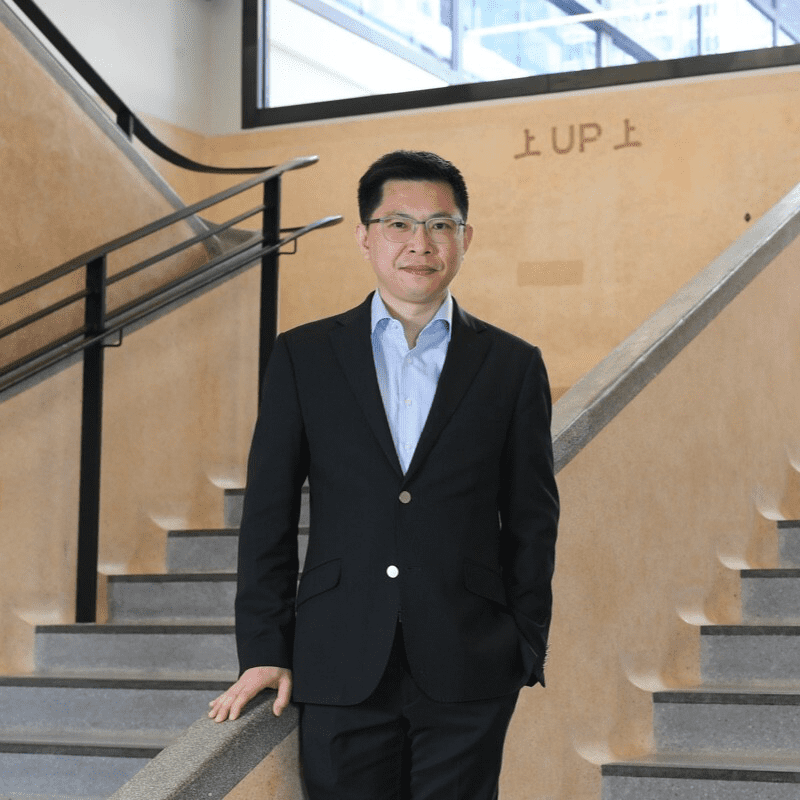
The collaboration with Ubudu has been effective and together we work toward excellence in every aspect of project delivery.
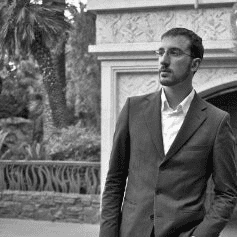
A simple solution to make operators aware of the areas of interaction with the machines.
What is the typical Return on Investment (ROI) of RTLS in a manufacturing plant?
The ROI of RTLS in a manufacturing plant depends on the use case and on the costs of the solution (especially cabling costs). Ubudu hybrid RTLS can be deployed with different technical architectures in order to optimise the costs of the solution based on the client needs. With this approach, the ROI is between 6 to 12 months.
How much time can operators save searching for work orders, tools & equipment?
The time spent by operators searching for assets in manufacturing and logistics plants have been reduced by 60-80%. This means that not only the operators have more time to spend on added-value operations and be more productive but it also revalues the work of operators by giving them the tools to be more efficient.
Can the data be integrated into MES, WMS and ERP systems?
Yes, Ubudu provides an open API that allows you to integrate real-time and historical data to your MES, WMS and ERP systems. There are 3 types of data that can be integrated: positions, entry/exit in zones and alerts. Automatisation can be done by defining actions to take place automatically in your system based on the data received from the Ubudu system.
How can I analyse the flow of my operations using RTLS?
The Analytics Dashboard enables you to create any type of graphic you want to analyse the flow of your operations. For example, you can create pie charts to quickly see how much time assets spend in different zones, you can make use of the flow diagram to see in which zones the asset went, you can create heatmaps to identify in which parts of the plant most assets go etc...