Cómo un proveedor del sector aeroespacial redujo su plazo de entrega mediante el seguimiento de las órdenes de trabajo
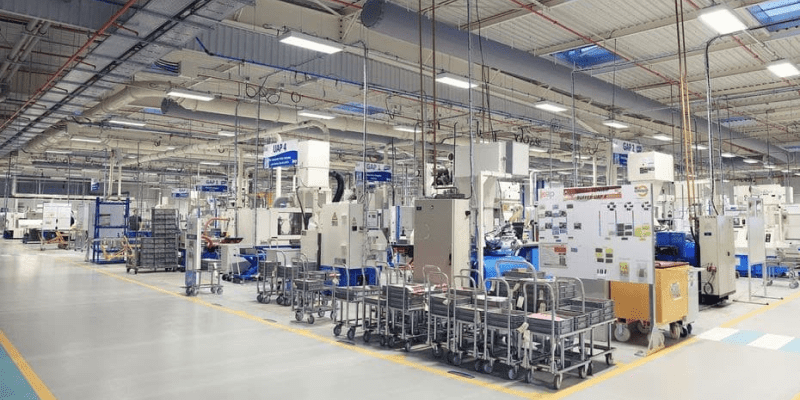
La duradera demanda de aviones comerciales exige que tanto los fabricantes como los proveedores aumenten su capacidad de producción. Un importante proveedor de piezas metálicas decidió afrontar este reto implantando una solución de seguimiento de órdenes de trabajo, que no solo reduciría el tiempo de espera entre etapas, sino que también proporcionaría una mejor visibilidad de las operaciones generales.
El tiempo de respuesta, un sinvivir de la guerra industrial
Tradicionalmente, la capacidad de producción se incrementa invirtiendo en nuevos recursos productivos (nuevas plantas, nuevas líneas, nuevas máquinas, etc.), pero ni siquiera los equipos más innovadores y eficientes pueden ser siempre la respuesta a todos los problemas industriales. Sobre todo cuando ya se ha realizado un esfuerzo inversor en este sentido.
El tiempo de espera entre las diferentes etapas de producción es un componente importante del TaT global, por lo que su reducción debe ser uno de los primeros objetivos. Permite aprovechar mejor los recursos existentes y ayuda a optimizar las futuras inversiones industriales.
Este es el caso de este proveedor de piezas metálicas, que necesitaba reducir su plazo de entrega de 16 a unas drásticas 6 semanas, para poder seguir el ritmo marcado por sus principales clientes, Airbus y Boeing. Para alcanzar este objetivo, cada segundo contaba y había que ahorrarlo. Y sin ninguna sorpresa, consideraron el tiempo de espera en prioridad, como un Despilfarro Lean Six Sigma que había que eliminar a toda costa..
Las máquinas son mejores que los humanos para actualizar los estados
Cuando el Director de Rendimiento Industrial analizó las razones de los tiempos de espera, encontró varias causas que coinciden bastante con el análisis de Herramientas de fabricación ajustada :
- Procesos desequilibrados, con tiempo de inactividad entre cada uno
- Procesos poco fiables, que provocan averías, mantenimiento y, por tanto, retrasos
- Cuellos de botella en la manipulación de materiales, cuando las carretillas elevadoras tienen que trasladar lotes de piezas desde el inventario hasta un puesto de trabajo de montaje
- Falta de información, cuando el estado de la orden de trabajo no está actualizado.
Ya se habían realizado optimizaciones en los 3 primeros, por lo que el principal factor de reducción del tiempo de espera era la "falta de información". En otras palabras, el estado y los detalles de las órdenes de trabajo no estaban actualizados.
Inicialmente, el fabricante comenzó a aplicar los principios de Lean Manufacturing, y utilizó papel l Tablas KanbanEn realidad, no se aleja tanto del modelo original de Toyota.
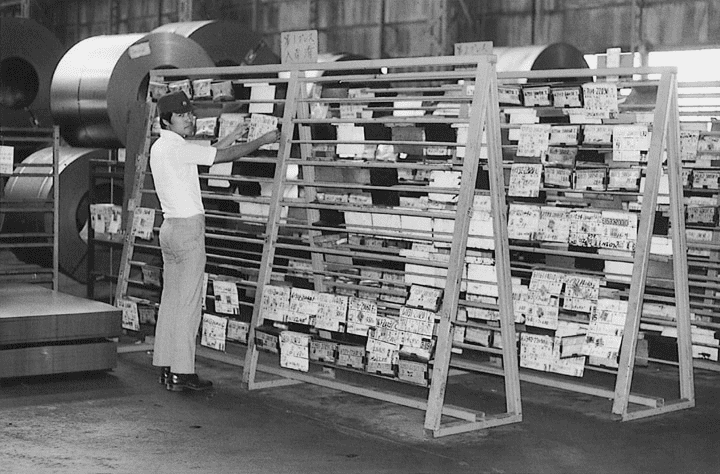
Esto estaba bien, pero con dos advertencias principales: en primer lugar, los operadores tenían que ir una y otra vez al tablero para recuperar la información, y en segundo lugar, la exactitud de la información dependía en gran medida de que los operadores introdujeran los datos correctamente y a tiempo.
A continuación, el fabricante pasó al tablero kanban digital, sustituyendo el ejercicio en papel por un sistema de código de barras. Ahora los operarios sólo tenían que escanear un código de barras en la orden de trabajo y un código de barras en el puesto de trabajo para actualizar el estado. La vista de Kanban podía digitalizarse y estar disponible para todos mediante un ordenador, sin tener que desplazarse hasta el tablero físico. Esto resolvió la primera advertencia inicial, pero no la de la integridad de los datos.
El cambio a Kanban automatizado mediante el seguimiento de las órdenes de trabajo
El director de rendimiento industrial conoció a Ubudu en una gran feria sobre la Industria 4.0 en París. Se sintió atraído por un cartel con el título "IoT for Lean". Allí nos explicó su problema de tiempo de espera y nos preguntó si nuestro sistema de seguimiento de activos podía ser una solución.
Sí, así es. Mediante el emparejamiento Etiquetas UWB a las cajas de plástico de las órdenes de trabajo, y localizándolas con precisión cuando entraban o salían de un puesto de trabajo o de la zona de existencias, pudimos tener una visión precisa y en tiempo real de todo el proceso de producción. Además, las alertas podían activarse automáticamente en caso de cualquier variación con respecto a la línea de base: tiempo de espera excesivo, tiempo de procesamiento excesivo, nivel de existencias excesivo o insuficiente, etc.
Además, algunas órdenes de trabajo podían almacenarse en zonas poco habituales, por falta de espacio. Tener acceso a su localización real se convirtió en una ventaja adicional, que permitió a los operarios ahorrar tiempo al no tener que buscarlas nunca más.
Teniendo en cuenta las 4.000 órdenes de trabajo que deben pasar por 9 unidades de producción durante un ciclo de producción, y 16 semanas de duración media por ciclo de producción, eso supone un ahorro de 260 horas, o unos 50.000 euros al año.
Además, tener la visibilidad en tiempo real de todo el proceso ayudó al fabricante a identificar nuevos puntos débiles en los que trabajar, dándole la herramienta para aplicar la mejora continua, en línea con su imperativo de aumentar la capacidad.
Víctor Hugo dijo una vez: "Atreverse es el precio del progreso". Por haberse atrevido a implantar una solución innovadora de IoT, este proveedor de piezas metálicas aeroespaciales había cimentado su relación con los fabricantes de aviones y reforzado su liderazgo en el mercado.
Noticias que pueden interesarle
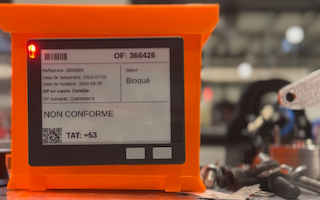
Integración de BLE ESL y RTLS en la fabricación
La integración BLE ESL de Ubudu con su RTLS ofrece seguimiento de activos en tiempo real y actualizaciones automatizadas para la fabricación. Con pantallas ESL dinámicas de marcas como PDI Digital y Minew -con opciones de tamaño, baterías intercambiables y protección contra golpes-, esta solución agiliza los flujos de trabajo mediante una red BLE inalámbrica, disponible a través de SaaS o in situ.
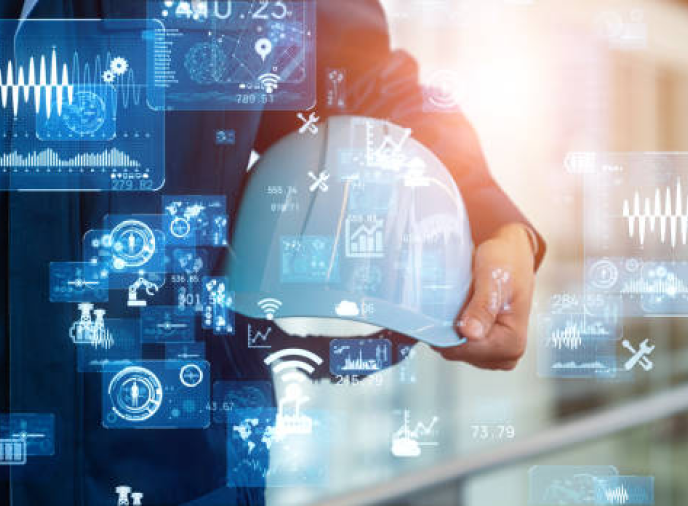
La potencia de las soluciones RTLS híbridas
El RTLS híbrido combina las ventajas de distintas tecnologías de localización para ofrecer los resultados más eficientes a las necesidades de seguimiento y puede utilizarse para múltiples casos de uso. A medida que el posicionamiento en interiores y exteriores se interconecta cada vez más, es importante considerar cómo combinar diferentes tecnologías RTLS para mejorar el retorno de la inversión y satisfacer las necesidades de los usuarios finales.
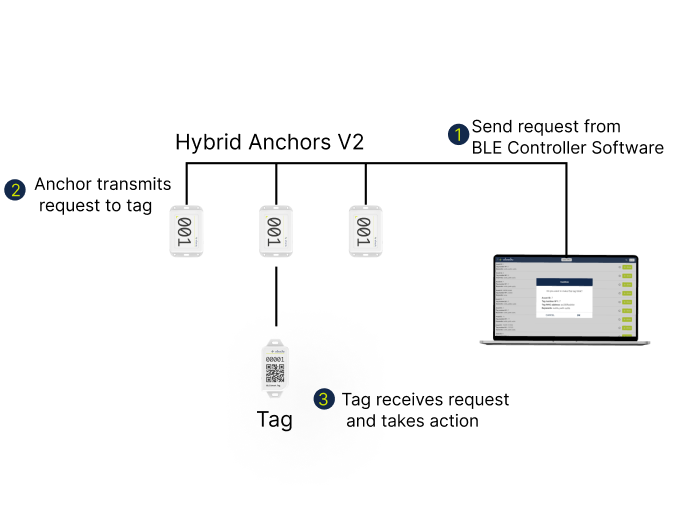
Introducción a Ubudu BLE Controller
Ubudu lanza "BLE Controller", una nueva función disponible en Ubudu RTLS que le permitirá comunicarse con cualquier RTLS tag de forma remota, directamente desde su escritorio.