Come un fornitore aerospaziale ha ridotto il suo Turn-around Time tracciando gli ordini di lavoro
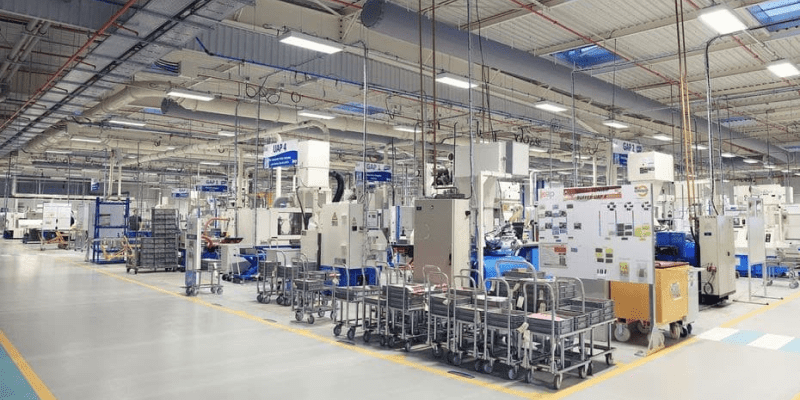
La continua domanda di aerei commerciali richiede sia ai produttori che ai fornitori di aumentare la loro capacità di produzione. Un fornitore leader di parti metalliche ha deciso di affrontare questa sfida implementando una soluzione di tracciamento degli ordini di lavoro, che non solo ridurrà i tempi di attesa tra le fasi, ma fornirà anche una migliore visibilità sulle operazioni complessive.
Turn-around Time, tendine della guerra industriale
La capacità produttiva viene tradizionalmente aumentata investendo in nuovi mezzi di produzione (nuovi impianti, nuove linee, nuove macchine, ecc.), ma anche le attrezzature più innovative ed efficienti non sempre possono essere la risposta a tutti i problemi industriali. Soprattutto quando lo sforzo di investimento in questa direzione era già stato fatto.
Il tempo di attesa tra le diverse fasi di produzione è una componente importante del TaT complessivo, e quindi la sua riduzione dovrebbe essere uno dei primi obiettivi. Permette di utilizzare meglio le risorse esistenti e di ottimizzare gli investimenti industriali futuri.
È il caso di questo fornitore di parti metalliche, che aveva bisogno di ridurre il suo tempo di consegna da 16 a un drastico 6 settimane, al fine di tenere il passo con i suoi principali clienti, Airbus e Boeing. Per raggiungere questo obiettivo, ogni secondo contava e doveva essere salvato. E senza alcuna sorpresa, si è guardato al tempo di attesa in priorità, come un Rifiuti Lean Six Sigma che doveva essere eliminato a tutti i costi.
Le macchine sono migliori degli umani nell'aggiornare gli stati
Quando l'Industrial Performance Manager ha analizzato le ragioni dei tempi di attesa, ha trovato diverse cause che sono abbastanza in linea con l'analisi di Strumenti di produzione snella :
- Processi sbilanciati, con tempo di inattività tra ciascuno
- Processi inaffidabili, che causano guasti, manutenzione e quindi ritardi
- Colli di bottiglia nella movimentazione dei materiali, quando i carrelli elevatori devono spostare lotti di pezzi dall'inventario a una stazione di lavoro di assemblaggio
- Mancanza di informazioni, quando lo stato dell'ordine di lavoro non è aggiornato.
Le ottimizzazioni sui primi 3 erano già state condotte, quindi il driver principale per la riduzione del tempo di attesa era "Mancanza di informazioni". In altre parole, lo stato e i dettagli degli ordini di lavoro non erano aggiornati.
Inizialmente il produttore ha iniziato ad applicare i principi del Lean Manufacturing, e ha usato la carta l Tavole Kanban, in realtà non così lontano dal modello originale Toyota.
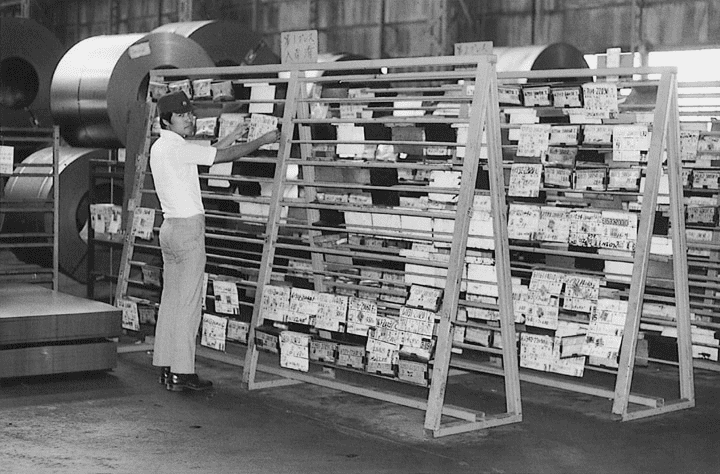
Questo andava bene, ma con due avvertenze principali: in primo luogo, gli operatori dovevano andare ripetutamente avanti e indietro alla lavagna per recuperare le informazioni, e in secondo luogo, l'accuratezza delle informazioni dipendeva molto dall'inserimento corretto e tempestivo dei dati da parte degli operatori.
Poi il produttore è passato al pannello kanban digitale, sostituendo l'esercizio cartaceo con un sistema di codici a barre. Gli operatori ora dovevano solo scansionare un codice a barre sull'ordine di lavoro e un codice a barre sulla stazione di lavoro, per aggiornare lo stato. La vista Kanban poteva ora essere digitalizzata e disponibile a tutti usando un computer, senza dover camminare fino alla lavagna fisica. Questo risolveva il primo problema iniziale, ma non quello dell'integrità dei dati.
Il passaggio al Kanban automatizzato usando il tracciamento degli ordini di lavoro
L'Industrial Performance Manager ha incontrato Ubudu in una grande fiera sull'Industria 4.0 a Parigi. È stato attratto da un poster con il titolo "IoT for Lean". Lì ci ha spiegato il suo problema dei tempi di attesa e ci ha chiesto se il nostro sistema di tracciamento degli asset poteva essere una soluzione.
Sì. Con l'accoppiamento Tag UWB alle scatole di plastica degli ordini di lavoro e localizzandoli accuratamente quando si spostavano da e verso una stazione di lavoro o un'area di magazzino, eravamo in grado di avere una visione accurata e in tempo reale dell'intero processo di produzione. Inoltre, gli avvisi potevano essere attivati automaticamente in caso di qualsiasi variazione rispetto alla linea di base: tempo di attesa eccessivo, tempo di lavorazione eccessivo, livello di scorte eccessivo o insufficiente, ecc.
Inoltre, alcuni ordini di lavoro potevano essere memorizzati in zone insolite, a causa della mancanza di spazio. Avere accesso alla loro effettiva localizzazione è diventato un ulteriore vantaggio, permettendo agli operatori di risparmiare tempo non dovendo più cercarli.
Considerando i 4.000 ordini di lavoro che devono passare attraverso 9 unità di produzione durante un ciclo di produzione, e 16 settimane di durata media per ciclo di produzione, questo è un risparmio di 260 ore, o circa 50.000 euro all'anno.
Inoltre, avere la visibilità in tempo reale sull'intero processo ha aiutato il produttore a identificare nuovi punti critici su cui lavorare, dandogli lo strumento per applicare il miglioramento continuo, in linea con il suo imperativo di aumentare la capacità.
Victor Hugo disse una volta: "Osare è il prezzo del progresso". Per aver osato implementare una soluzione IoT innovativa, questo fornitore di componenti metallici per l'aerospazio ha consolidato il suo rapporto con i produttori di aeromobili e ha rafforzato la sua leadership sul mercato.
Notizie che potrebbero interessarti
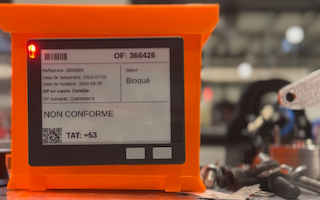
Integrazione di BLE ESL e RTLS nella produzione
L'integrazione BLE ESL di Ubudu con il suo RTLS offre la tracciabilità degli asset in tempo reale e gli aggiornamenti automatizzati per la produzione. Con display ESL dinamici di marchi come PDI Digital e Minew - con opzioni di dimensioni, batterie intercambiabili e protezione dagli urti - questa soluzione ottimizza i flussi di lavoro utilizzando una rete BLE wireless, disponibile via SaaS o on-premise.
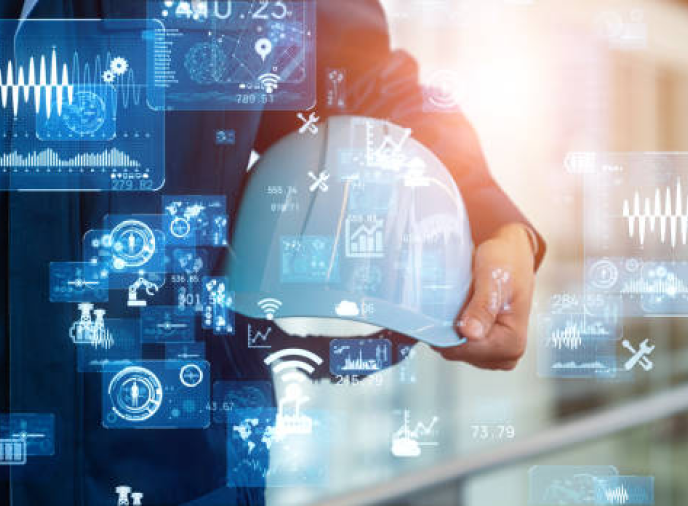
La potenza delle soluzioni RTLS ibride
L'RTLS ibrido combina i vantaggi di diverse tecnologie di localizzazione per fornire i risultati più efficienti per le esigenze di localizzazione e può essere utilizzato per diversi casi d'uso. Poiché il posizionamento all'interno e all'esterno diventa sempre più interconnesso, è importante considerare come combinare diverse tecnologie RTLS per migliorare il ROI e soddisfare le esigenze degli utenti finali.
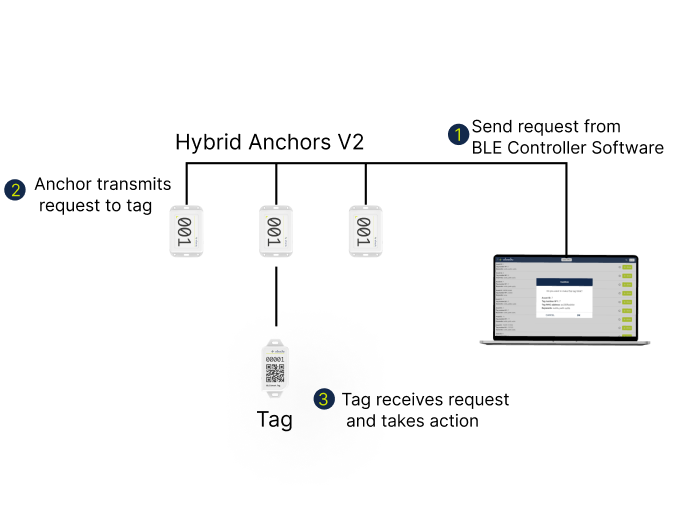
Introduzione a Ubudu BLE Controller
Ubudu lancia "BLE Controller", una nuova funzione disponibile in Ubudu RTLS che vi permetterà di comunicare con qualsiasi RTLS tag da remoto, direttamente dalla vostra scrivania.