Wie ein Luft- und Raumfahrtzulieferer seine Durchlaufzeit durch die Verfolgung von Arbeitsaufträgen verkürzte
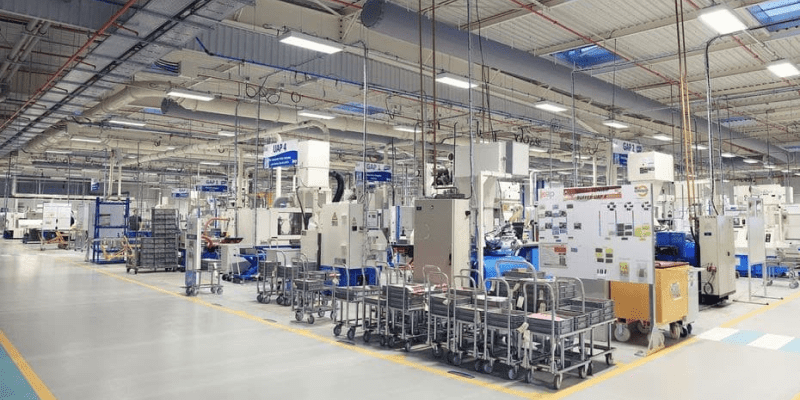
Die anhaltende Nachfrage nach Verkehrsflugzeugen erfordert sowohl von den Herstellern als auch von den Zulieferern eine Erhöhung ihrer Produktionskapazität. Ein führender Zulieferer von Metallteilen beschloss, diese Herausforderung durch die Einführung einer Lösung zur Verfolgung von Arbeitsaufträgen zu bewältigen, die nicht nur die Wartezeit zwischen den einzelnen Arbeitsschritten verkürzt, sondern auch einen besseren Überblick über die Gesamtabläufe bietet.
Turn-around Time, Sehne des industriellen Krieges
Die Produktionskapazität wird traditionell durch Investitionen in neue Produktionsmittel (neue Anlagen, neue Linien, neue Maschinen usw.) erhöht, aber selbst die innovativsten und effizientesten Anlagen können nicht immer die Antwort auf alle industriellen Probleme sein. Vor allem dann nicht, wenn bereits Investitionen in diese Richtung getätigt worden sind.
Die Wartezeit zwischen den verschiedenen Produktionsschritten ist ein wesentlicher Bestandteil der Gesamt-TaT, und daher sollte ihre Verringerung eines der ersten Ziele sein. Sie ermöglicht eine bessere Nutzung der vorhandenen Ressourcen und trägt zur Optimierung künftiger industrieller Investitionen bei.
Dieser Zulieferer von Metallteilen musste seine Durchlaufzeit von 16 auf drastische 6 Wochen verkürzen, um mit dem Tempo seiner wichtigsten Kunden Schritt zu halten, Airbus und Boeing. Um dieses Ziel zu erreichen, zählte jede Sekunde und musste eingespart werden. Und ohne jede Überraschung betrachteten sie die Wartezeit vorrangig als ein Lean Six Sigma-Verschwendung die um jeden Preis beseitigt werden muss.
Maschinen sind besser als Menschen bei der Aktualisierung von Statusmeldungen
Als der Industrial Performance Manager die Gründe für die Wartezeiten analysierte, fand er mehrere Ursachen, die sich ziemlich genau mit der Analyse von Werkzeuge der schlanken Produktion :
- Unausgewogene Prozesse, mit Leerlaufzeit zwischen den einzelnen Prozessen
- Unzuverlässige Prozesse, die zu Ausfällen, Wartungsarbeiten und damit zu Verzögerungen führen
- Engpässe im Materialtransport, wenn Gabelstapler Teile aus dem Lager zu einem Montagearbeitsplatz transportieren müssen
- Informationsmangel, wenn der Status des Arbeitsauftrags nicht auf dem neuesten Stand ist.
Bei den ersten drei Aufträgen waren bereits Optimierungen durchgeführt worden, so dass der Hauptgrund für die Verkürzung der Wartezeit "Informationsmangel" war. Mit anderen Worten: Der Status und die Details des Arbeitsauftrags waren nicht auf dem neuesten Stand.
Ursprünglich begann der Hersteller mit der Anwendung von Lean-Manufacturing-Prinzipien und verwendete Papier. Kanban-TafelnDas ist eigentlich gar nicht so weit vom ursprünglichen Toyota-Modell entfernt.
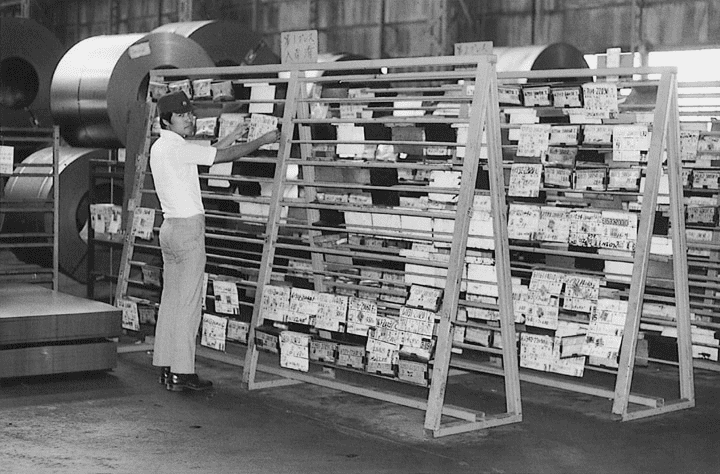
Das war in Ordnung, hatte aber zwei wesentliche Nachteile: Erstens mussten die Bediener immer wieder zur Tafel zurückkehren, um die Informationen abzurufen, und zweitens hing die Genauigkeit der Informationen stark von der korrekten und rechtzeitigen Dateneingabe durch die Bediener ab.
Dann ging der Hersteller zur digitalen Kanbantafel über, indem er die Papierübung durch ein Barcodesystem ersetzte. Die Mitarbeiter mussten nun nur noch einen Barcode auf dem Arbeitsauftrag und einen Barcode auf der Arbeitsstation scannen, um den Status zu aktualisieren. Die Kanban-Ansicht konnte nun digitalisiert werden und stand allen Mitarbeitern über einen Computer zur Verfügung, ohne dass sie zur physischen Tafel gehen mussten. Damit war das erste Problem gelöst, nicht jedoch das der Datenintegrität.
Die Umstellung auf automatisiertes Kanban durch die Verfolgung von Arbeitsaufträgen
Der Industrial Performance Manager traf Ubudu auf einer großen Fachmesse zum Thema Industrie 4.0 in Paris. Er wurde von einem Plakat mit der Überschrift "IoT for Lean" angezogen. Dort erklärte er uns sein Wartezeitproblem und fragte, ob unser Asset-Tracking-System eine Lösung sein könnte.
Ja, das war es. Durch die Kopplung UWB-Tags an die Plastikboxen der Arbeitsaufträge und deren genaue Lokalisierung beim Betreten oder Verlassen einer Arbeitsstation oder eines Lagerbereichs konnten wir einen genauen Überblick über den gesamten Produktionsprozess in Echtzeit erhalten. Darüber hinaus konnten bei Abweichungen von der Basislinie automatisch Warnmeldungen ausgelöst werden: übermäßige Wartezeit, übermäßige Bearbeitungszeit, übermäßiger oder unzureichender Lagerbestand, usw.
Außerdem konnten einige Arbeitsaufträge aus Platzmangel in ungewöhnlichen Zonen gespeichert werden. Der Zugang zu ihrer tatsächlichen Lokalisierung wurde zu einem zusätzlichen Vorteil, der es den Bedienern ermöglichte, Zeit zu sparen, da sie nicht mehr danach suchen mussten.
Angesichts von 4.000 Arbeitsaufträgen, die während eines Produktionszyklus 9 Produktionseinheiten durchlaufen müssen, und einer durchschnittlichen Dauer von 16 Wochen pro Produktionszyklus bedeutet dies eine Einsparung von 260 Stunden oder etwa 50.000 Euro pro Jahr.
Darüber hinaus half die Echtzeittransparenz des gesamten Prozesses dem Hersteller, neue Schwachstellen zu erkennen, an denen er arbeiten konnte, und gab ihm das Werkzeug für eine kontinuierliche Verbesserung in Übereinstimmung mit seiner Notwendigkeit, die Kapazität zu erhöhen.
Victor Hugo sagte einmal: "Wage es, das ist der Preis für den Fortschritt". Weil er es gewagt hat, eine innovative IoT-Lösung zu implementieren, hat dieser Zulieferer von Metallteilen für die Luft- und Raumfahrt nun seine Beziehungen zu den Flugzeugherstellern gefestigt und seine Marktführerschaft ausgebaut.
Nachrichten, die Sie interessieren könnten
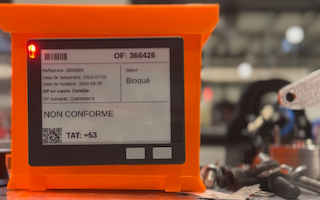
BLE ESL und RTLS-Integration in der Fertigung
Die ESL von Ubudu mit seinem RTLS liefert Echtzeit-Anlagenverfolgung und automatische Updates für die Fertigung. Mit dynamischen ESL von Marken wie PDI Digital und Minew - mit Optionen in Bezug auf Größe, austauschbare Batterien und Stoßschutz - rationalisiert diese Lösung Arbeitsabläufe mit einem drahtlosen BLE-Netzwerk, das über SaaS oder vor Ort verfügbar ist.
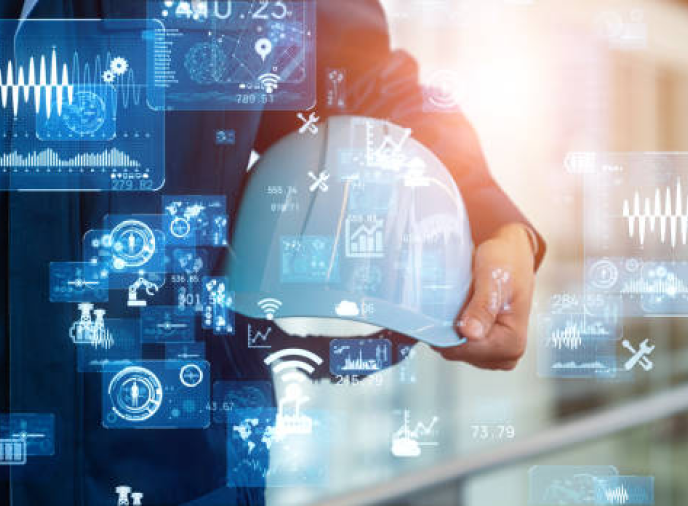
Die Leistungsfähigkeit von Hybrid-RTLS-Lösungen
Hybrid-RTLS kombiniert die Vorteile verschiedener Ortungstechnologien, um die effizientesten Ergebnisse bei der Ortung zu erzielen, und kann für mehrere Anwendungsfälle eingesetzt werden. Da die Positionierung in Innenräumen und im Freien zunehmend miteinander verbunden wird, ist es wichtig zu überlegen, wie verschiedene RTLS-Technologien kombiniert werden können, um den ROI zu verbessern und die Bedürfnisse der Endnutzer zu erfüllen.
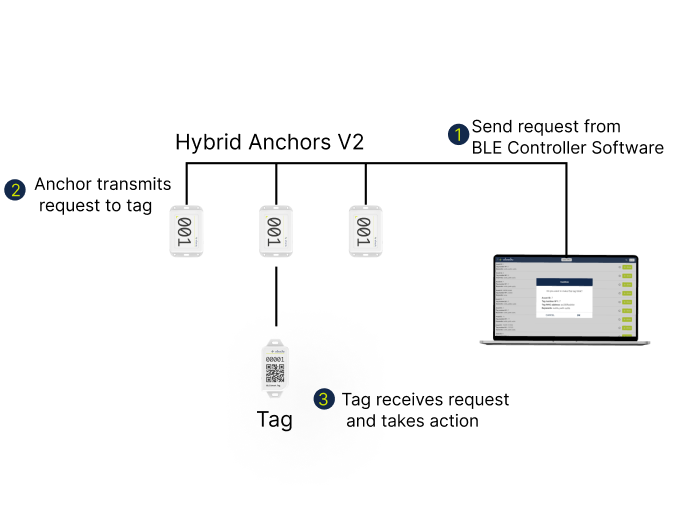
Einführung in Ubudu BLE Controller
Ubudu führt "BLE Controller" ein, eine neue Funktion in Ubudu RTLS, die es Ihnen ermöglicht, mit jedem RTLS tag aus der Ferne zu kommunizieren, direkt von Ihrem Schreibtisch aus.