Comment un fournisseur de l'industrie aérospatiale a réduit son délai d'exécution en suivant les ordres de fabrication.
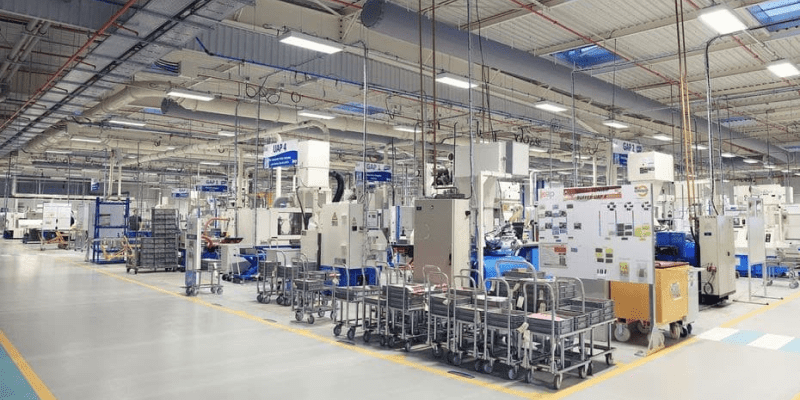
La demande durable d'avions commerciaux oblige les fabricants et les fournisseurs à augmenter leur capacité de production. Un important fournisseur de pièces métalliques a décidé de relever ce défi en mettant en œuvre une solution de suivi des ordres de fabrication, qui non seulement réduirait le temps d'attente entre les étapes, mais fournirait également une meilleure visibilité sur l'ensemble des opérations.
Le délai d'exécution, nerf de la guerre industrielle
La capacité de production est traditionnellement augmentée en investissant dans de nouveaux moyens de production (nouvelles usines, nouvelles lignes, nouvelles machines, etc.), mais même les équipements les plus innovants et les plus efficaces ne peuvent pas toujours être la réponse à tous les problèmes industriels. Mais même les équipements les plus innovants et les plus efficaces ne peuvent pas toujours répondre à tous les problèmes industriels. Surtout lorsque des efforts d'investissement dans cette direction ont déjà été réalisés.
Le site temps d'attente entre les différentes étapes de production est une composante majeure du TAD global, et sa réduction doit donc être l'un des premiers objectifs. Elle permet de mieux utiliser les ressources existantes et d'optimiser les futurs investissements industriels.
C'est le cas de ce fournisseur de pièces métalliques, qui devait réduire son délai d'exécution de 16 à 6 semaines, afin de suivre le rythme imposé par ses principaux clients, Airbus et Boeing. Pour atteindre cet objectif, chaque seconde comptait et devait être économisée. Et c'est sans surprise qu'ils ont considéré le temps d'attente en priorité, comme une Lean Six Sigma gaspillage qui doit être supprimé à tout prix .
Les machines sont meilleures que les humains pour mettre à jour les statuts
Lorsque le responsable de la performance industrielle a analysé les raisons des temps d'attente, il a trouvé plusieurs causes qui correspondent assez bien à l'analyse faite par le responsable de la performance industrielle. Lean industrie Tools :
- Processus déséquilibrés, avec des temps morts entre chaque processus.
- Des processus peu fiables, entraînant des pannes, de la maintenance, et donc des retards
- les goulets d'étranglement liés à la manutention, lorsque des chariots élévateurs doivent déplacer des lots de pièces du stock vers un poste de travail d'assemblage
- Manque d'information, lorsque le statut du bon de travail n'est pas à jour.
Les optimisations sur les 3 premiers avaient déjà été effectuées, donc le principal facteur de réduction du temps d'attente était le "manque d'information". En d'autres termes, l'état et le détail des bons de travail n'étaient pas à jour.
Au départ, le fabricant a commencé à appliquer les principes de l'industrie allégée et a utilisé des tableaux Kanban en papier. tableaux Kanban en papierEn fait, cette méthode n'est pas très éloignée du modèle original de Toyota.
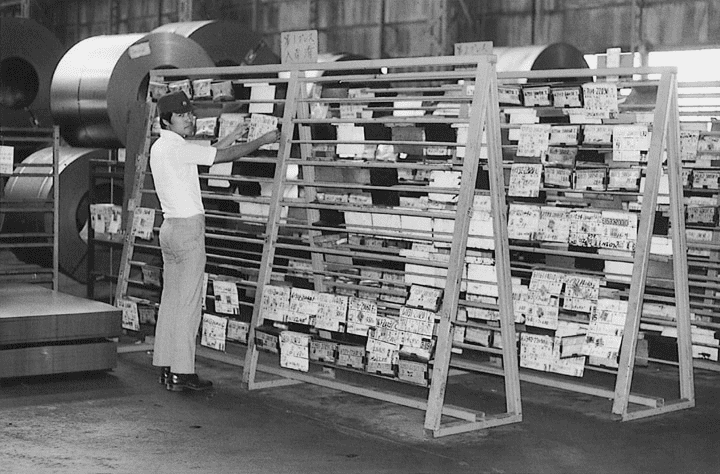
Cette méthode était acceptable, mais avec deux inconvénients majeurs : premièrement, les opérateurs devaient faire des allers-retours répétés vers le tableau pour récupérer les informations, et deuxièmement, la précision des informations dépendait fortement de la saisie correcte et rapide des données par les opérateurs.
Puis le fabricant est passé au tableau Kanban numérique, en remplaçant l'exercice papier par un système de code-barres. Les opérateurs n'avaient plus qu'à scanner un code-barres sur le bon de travail et un code-barres sur le poste de travail pour mettre à jour le statut. La vue Kanban pouvait désormais être numérisée et accessible à tous à l'aide d'un ordinateur, sans avoir à se déplacer jusqu'au tableau physique. Cela a permis de résoudre le premier problème initial, mais pas celui de l'intégrité des données.
Le passage au Kanban automatisé grâce au suivi des bons de travail
Le responsable de la performance industrielle a rencontré Ubudu lors d'un grand Salon professionnel sur l'industrie 4.0 à Paris. Il a été attiré par une affiche dont le titre était "IoT for Lean". Là, il nous a expliqué son problème de temps d'attente, et a demandé si notre système de suivi des actifs pouvait être une solution.
Oui, c'est vrai. En s'appariant lestags UWB aux boîtes en plastique des OFs et en les localisant avec précision lorsqu'ils entrent ou sortent d'un poste de travail ou d'une zone de stockage, nous avons pu avoir une vue précise et en temps réel de l'ensemble du processus de production. De plus, des alertes pouvaient être déclenchées automatiquement en cas de variation par rapport à la ligne de base : temps d'attente excessif, temps de traitement excessif, niveau de stock excessif ou insuffisant, etc.
En outre, certains bons de travail pouvaient être stockés dans des zones inhabituelles, par manque de place. Avoir accès à leur localisation réelle est devenu un avantage supplémentaire, permettant aux opérateurs de gagner du temps en n'ayant plus à les rechercher.
Compte tenu des 4 000 ordres de travail qui doivent passer par 9 unités de production au cours d'un cycle de production, et de la durée moyenne de 16 semaines par cycle de production, cela représente une économie de 260 heures, soit environ 50 000 euros par an.
En outre, le fait d'avoir une visibilité en temps réel sur l'ensemble du processus a permis au fabricant d'identifier de nouveaux points sensibles sur lesquels travailler, lui donnant ainsi l'outil nécessaire pour appliquer l'amélioration continue, conformément à son impératif d'augmentation de la capacité.
Victor Hugo a dit un jour "Osez, c'est le prix du progrès". Pour avoir osé mettre en œuvre une solution IoT innovante, ce fournisseur de pièces métalliques pour l'aéronautique avait désormais cimenté sa relation avec les avionneurs et renforcé son leadership sur le marché.
D'autres actualités qui pourraient vous intéresser
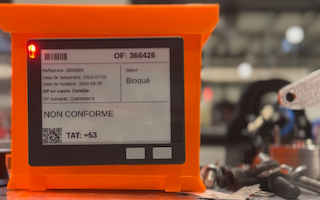
Intégration du BLE ESL et de la géolocalisation indoor (RTLS) dans l'industrie
L'intégration de l'ESL BLE d'Ubudu avec sa géolocalisation indoor (RTLS) permet un suivi en temps réel des actifs et des mises à jour automatisées pour l'industrie. Avec des écrans ESL dynamiques de marques telles que PDI Digital et Minew - avec des options de taille, des batteries interchangeables et une protection contre les chocs - cette solution rationalise les flux de travail en utilisant un réseau BLE sans fil, disponible via SaaS ou sur site.
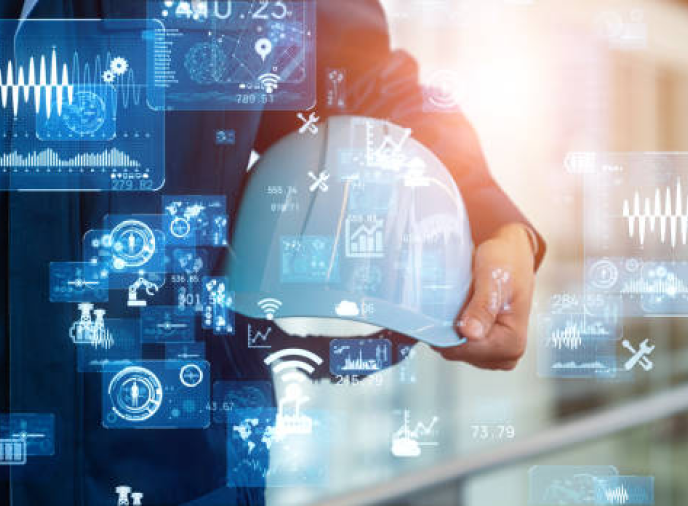
La puissance des solutions de géolocalisation indoor hybrides (hybride RTLS)
Le système de géolocalisation indoor hybride (hybride RTLS) combine les avantages de différentes technologies de localisation afin de fournir les résultats les plus efficaces pour les besoins de localisation et peut être utilisé pour de multiples cas d'utilisation. Le positionnement à l'intérieur et à l'extérieur devenant de plus en plus interconnecté, il est important de réfléchir à la manière de combiner différentes technologies la géolocalisation indoor (RTLS) pour améliorer le retour sur investissement et répondre aux besoins des utilisateurs finaux.
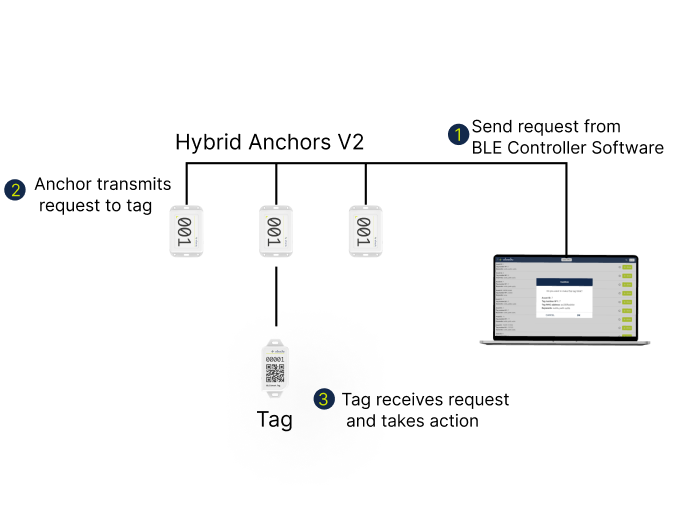
Introduction au BLE Controller de Ubudu
Ubudu lance "BLE Controller", une nouvelle fonctionnalité disponible dans le système de géolocalisation indoor d'Ubudu (RTLS) qui vous permettra de communiquer avec n'importe quel tag RTLS à distance, directement depuis votre bureau.